fochie
New member
Just "completed" an install of a Baldwin Ironworks cat delete pipe on my 2020 RTL.
Having a hard time getting a good seal from the cat delete pipe to the final (stock) muffler.
Very little of the cat delete ball shaped end fits into the final muffler and the factory clamp bottoms out as well.
Tried moving the clamp around several times but it was still leaking.
Last ditch effort was to goop on some high temp JB Weld Exhaust Seal to both parts and re-clamping it.
I let it dry for about an hour, checked it for leaks, and idled the bike for 10 mins (as per instructions).
It doesn't appear to be leaking now, but I have zero confidence that this is a lasting remedy. Have not ridden the bike since yet.
I spent WAY too much time prepping and installing the pipe (wrapped it and clamped it with fiberglass, sprayed it with high temp silicone, baked it at 400°, etc.) not to mention fighting with the dreaded top spring.
When first dry fitting the pipe, I noticed a miss-alignment with the cat delete pipe and the stock exhaust donut gasket (see pics). At the time, I sent pics and talked with Paul at Baldwin Ironworks (nice guy) and he advised it would be fine since the springs should make it seal ok. It doesn't appear to be leaking... at idle anyway. This was prior to realizing the issue with the connection to the final muffler.
We have a day ride coming up for the 4th this week, then a couple days trip next week, then a week long trip to Colorado at the end of the month. Contemplating putting the cat back on, if this hacked fix doesn't work out before the Colorado trip.
Since BOTH ends of the cat delete pipe do not marry up very well with the stock parts (especially the final muffler connection) I'm thinking of chalking this install up to lessons learned and buying an RLS cat delete muffler and hoping I don't run into the same problem.
So I'm wondering if anyone else has had similar fitment issues with this pipe; and/or any advice on a fix; or thoughts on the RLS pipe fitting better.
Thanks!!
Steve
- 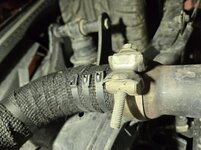
- 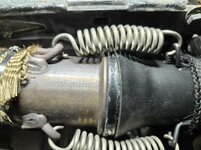
Having a hard time getting a good seal from the cat delete pipe to the final (stock) muffler.
Very little of the cat delete ball shaped end fits into the final muffler and the factory clamp bottoms out as well.
Tried moving the clamp around several times but it was still leaking.
Last ditch effort was to goop on some high temp JB Weld Exhaust Seal to both parts and re-clamping it.
I let it dry for about an hour, checked it for leaks, and idled the bike for 10 mins (as per instructions).
It doesn't appear to be leaking now, but I have zero confidence that this is a lasting remedy. Have not ridden the bike since yet.
I spent WAY too much time prepping and installing the pipe (wrapped it and clamped it with fiberglass, sprayed it with high temp silicone, baked it at 400°, etc.) not to mention fighting with the dreaded top spring.
When first dry fitting the pipe, I noticed a miss-alignment with the cat delete pipe and the stock exhaust donut gasket (see pics). At the time, I sent pics and talked with Paul at Baldwin Ironworks (nice guy) and he advised it would be fine since the springs should make it seal ok. It doesn't appear to be leaking... at idle anyway. This was prior to realizing the issue with the connection to the final muffler.
We have a day ride coming up for the 4th this week, then a couple days trip next week, then a week long trip to Colorado at the end of the month. Contemplating putting the cat back on, if this hacked fix doesn't work out before the Colorado trip.
Since BOTH ends of the cat delete pipe do not marry up very well with the stock parts (especially the final muffler connection) I'm thinking of chalking this install up to lessons learned and buying an RLS cat delete muffler and hoping I don't run into the same problem.
So I'm wondering if anyone else has had similar fitment issues with this pipe; and/or any advice on a fix; or thoughts on the RLS pipe fitting better.
Thanks!!
Steve
![20250628_145150[1]_min.jpg 20250628_145150[1]_min.jpg](https://www.spyderlovers.com/data/attachments/158/158376-afb3374817e2dd8c168ff2410bbe59b0.jpg?hash=GR2qYY610j)
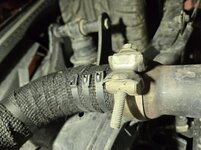
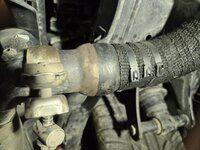
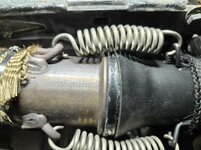